2019 Construction Costs: where are we and what we can do about it
- Rick Fourie, CCM
- Jan 9, 2019
- 4 min read
Updated: Oct 23, 2019

The basis of this article came from a simple side-project; come up with a US construction escalation prediction for 2019, write it in the form of a “Happy New Year” email, and hit “send.” However, the more I updated my data, dissected economic reports, squinted at graphs, compared, overlaid, and tried to figure out what the hell happened in 2003, a more complete image of the construction market emerged.
Construction costs are currently at a record high. The question becomes: Will this bubble burst?
I began with the following assumption: “over a long period, construction cost escalation must fall in line with inflation and GDP growth.” To test that theory, I took $100 and “construction escalated” it, "inflationed" it, and “GDP’d” it, dating back from January 1985 through to January 2019. I graphed the results below:

The challenge in predicting construction costs is that there is never a fixed price. If you specify a door and hardware set and send that to five different suppliers, you will get back five different quotes – sometimes significantly different. The same goes for steel, concrete, HVAC, and electric, all the trades. Despite the challenges, this also creates opportunities. By using some basic logic and a little more leg-work, you can receive a qualified bid on the same building for 10% less!
I have come to learn that a good estimate is an accurate synthesis of thousands of errors; hopefully, those are small errors that do not add up to collateral losses. To draw the most accurate blue line for construction costs, I used information from Ed Zarenski, Turner Construction Cost Index, Beck Biannual Cost Report, Mortenson Cost Index, RS Means, and my independent data/notes from 25 years of working on more than $20 billion in construction in 40 US States, 10 countries, and 4 continents. The Turner and Beck information was the most heavily weighted.
Notice the 2008 spike, which saw a rise from 2004 at about 7.5% per year to a high of 17.5% above the inflation/GDP benchmark. For the current “spike” we have seen another rise (from 2012) at about 4.5% per year to a record high of 19.5% above benchmark. Not even the drastic 12.5% drop experienced during the great recession would take us back to the benchmark numbers seen in 2010 - 2012.
Does this mean that the construction bubble will burst? Nobody knows. However, the data does suggest more volatility, with higher than benchmark prices as a general trend. Although market corrections may temporarily drop prices, barring an international catastrophe worse than the great recession, these prices are the new reality.

The root causes of these high prices are labor and productivity, because the fact of the matter is commodities are stable. There is no need to rehash the discussion about labor shortages; everyone in the industry knows about that. What I do want to emphasize is that Productivity Trends shows a decrease in productivity. Historically, both productivity and escalation were relatively constant, until 2003 when escalation in productivity indicators started to go all over the place.
The short story: We require skilled labor. Our own industry training programs and vocational schools do not prepare enough graduates who are interested in our industry to meet the demand. And the situation is not improving, given that more boomers are retiring.
To combat the labor shortage, we need to support vocational programs, legal immigration, and young women in construction. The best stone mason I have worked with came from Turkey and the best electrician from the Philippines. Any person who will walk a thousand miles for a better life for their kids will not be stopped by metaphorical or literal walls. Moreover, NAWIC is a great organization, and it is up to each of us to encourage and support every member of our team, regardless of their gender. We should break the stereotype that construction is a “man’s job” and encourage young women to learn a trade.
Industry advances have also started to reduce construction costs. Prefabrication is becoming more popular and enables project leaders to streamline the overall construction schedule. BIM use is also spreading; this allows a much larger subcontractor base to be competitive when coupled with off-site fabrication.
Broadly speaking, productivity is key. We must invest in technology and training programs to improve productivity to help offset the labor shortage that won’t go away anytime soon.
It is not an overstatement to say that the last 15 years have been the most transformative in our industry since the invention of the wheel. No doubt, the next 15 years will be filled with innovations that we cannot even imagine at present. We have continually moved away from the traditional design-bid-build delivery method. The best bid results will always come from competitive bids between educated and engaged subcontractors on a well-coordinated bid document set. When selecting a delivery method, better coverage and a fair and open competition for subcontractors will continue to deliver better bid results.
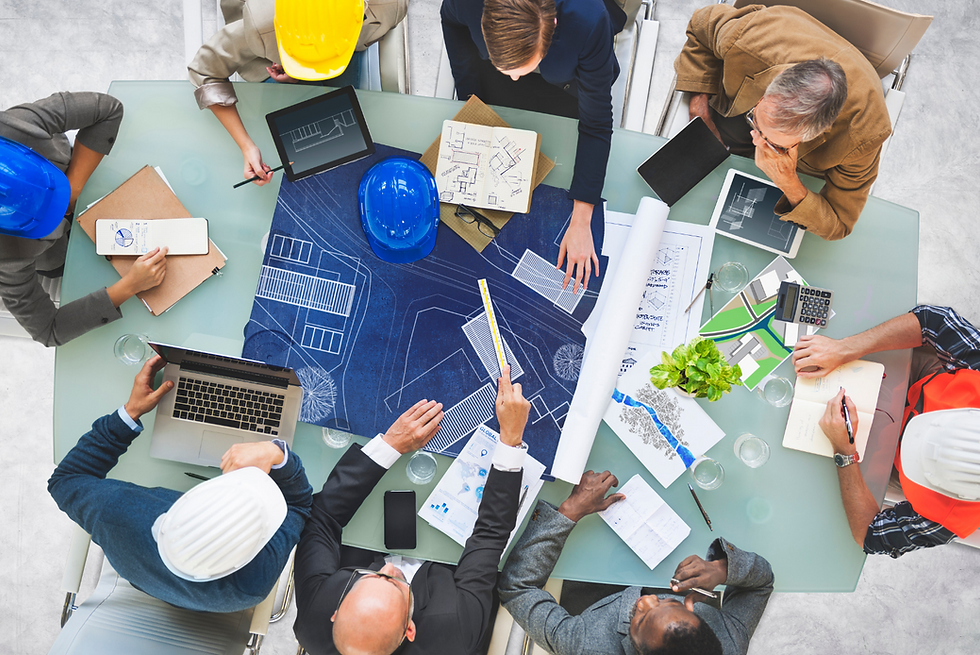
Ultimately, forces outside of our control are influencing the construction industry and the rise in construction costs is the result. It is a general trend that will continue, even if we see slowdowns and other corrections. That being said, we are not powerless to counter the effects of this rising tide, and I hope this article will contribute to a healthy discussion. Perhaps my next article should be titled “How to bid your project below budget?” On that note, my recommendation is to budget 3% for cost escalation in 2019!
Comentarios